Machine Parts
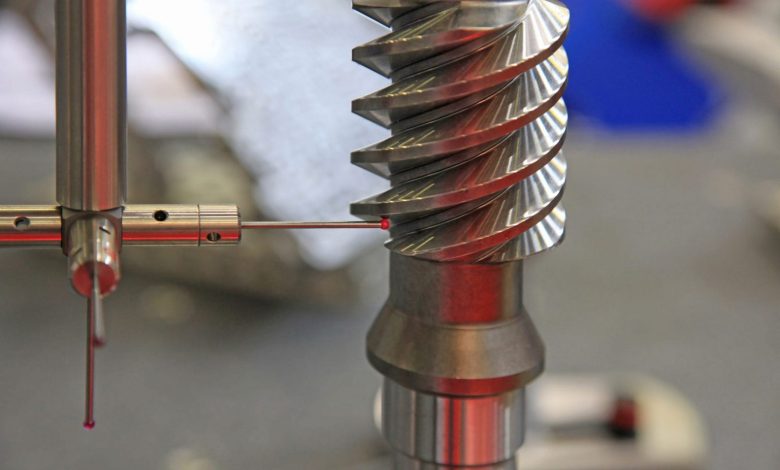
What are machine parts?
These components consist of three essential sorts: primary parts like casing individuals, direction, axles, splines, clasp, seals, and oils, components that control development in different ways, for example, gear trains, belt or chain drives, linkages, cam and supporter frameworks, including brakes and grasps.
What are mechanical parts?
For mechanical parts and machine parts
Fundamentally, the motivation behind mechanical parts is to take input power and change it through the mix of different machine components like pinion wheels, direction, rotaries, and different parts. In proficiently working hardware, mechanical parts decrease erosion and convey loads for straight or turning movement.
What are standard parts?
A standard part is any part that can reuse or “normalized” across a get-together or various congregations. Standard parts incorporate clasps, sections, chambers, or even whole congregations of parts. Expanding the utilization of standard parts and their applications will skyrockets configuration speed and proficiency for engineers.
What is the machine part plan?
Portrayal. Considered a norm in the course, Juvinall and Marshek’s Machine Part Configuration keeps on zeroing in on the basics of part plan – – free body graphs, force stream ideas, disappointment speculations, and exhaustion plan, with applications to clasp, springs, heading, cogwheels, grasps and brakes. Explore investment casting US
How are machine parts made?
Machined parts are cut from strong bits of material known as spaces, which have normally been projected or expelled. This makes them exceptionally amazing contrasted with, for instance, 3D printed parts, which can be a lot more fragile along one hub where one layer is based upon the following.
What are the fundamental parts of mechanical frameworks?
There are three essential actual components that makeup interpreting mechanical framework: latency components, springs, and grinding components.
What are the hindrances of casting?
Burdens of Casting
A high tooling cost and a long set-up time.
The super durable mold casting process is, as a general rule, restricted to more modest castings.
In light of the great tooling cost included, a high creation volume requires to make this cycle a financially reasonable assembling choice.
Mold making
In this phase of the sand projecting cycle, a headstrong material is load or pressed on the cup, stuffed around the example still it completely compacted. The example is then taken out leaving the shape in the mold pit. The sand used to make is mold is sufficiently able to hold the heaviness of the liquid metal when it is poured and should adequately weak to be broken while the projecting cool and set. Dirt and some synthetic holding specialist are utilized to fortify the mold to endure the pouring.
Assuming the sand is stuffed in the adapt. And haul while the example is in it, the adapt and drag are isolated with the goal that the example can undoubtedly be taken out. A headstrong covering is added to the outer layer of the cavity to create a superior surface completion and to permit the mold to endure the poured metal. The jar is coupled back together, for leaving the shape in the depression.
What is the most well-known material utilized for casting?
Normal casting metals are aluminum, magnesium, and copper combinations. Different materials incorporate tin, zinc, and lead composites, and iron and steel are likewise projected in graphite molds. Long-lasting molds, while enduring more than one casting still have a restricted life prior to breaking down
1) Pressure Molding
The pressure molding process is utilized to make elastic and plastic parts. In the elastic pressure molding process, a preformed part of the elastic is put in a warmed mold, then, at that point, the mold is shut and held under tension until the elastic takes the state of depression and vulcanizes. Vacuum-helped pressure molding is comparable however positioned under a vacuum to eliminate any gases. What’s more, guarantees the most ideal mold filling and shape adherence.
Pressure molding offers a few advantages over other molding processes, including low tooling expenses and quick lead times. In any case, the cycle requires manual treatment of the mold and items, bringing about more slow process durations.
2) Liquefy Molding
When applied to thermoplastic materials, pressure molding is alluded to as liquefy molding. For this manufacturing strategy. The polymers are warmed over their liquefying point, so they can expect a fluid structure.
The subsequent polymer is then permitted to cool. And set as the mold. At the point when temperature conditions are appropriately controlled, dissolve molding can convey preferable mechanical properties over pressure molding.
3) Move Molding
During the time spent move molding, the material is stacked into a chamber preceding being constrained into the mold. The chamber might be in the molding machine or in the actual mold. Move molding might utilize elastic or plastics, albeit the cycle for every material is unique. Tooling calculations are a smidgen more mind-boggling than pressure molding yet display lower cost than infusion molding.
4) Infusion Molding
The infusion molding interaction can utilize with both thermoplastic materials and thermosets. Infusion molding machines infuse liquid polymer materials under high tensions and paces into shut molds. However, making these molds can be more costly, the cycle can at last give completed parts at a high creation rate.
Advantages Of Hiring A Professional To Write Your Assignment